Continuous improvement: everything you should know
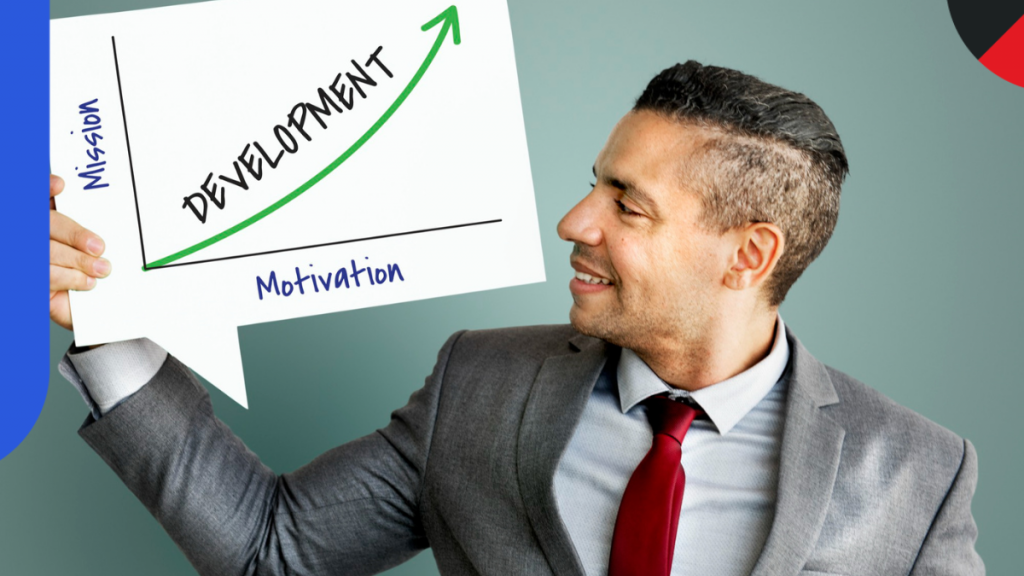
Conteúdo
Within a market in constant transformation and customers getting more and more demanding in relation to what brands have to offer, it is natural that companies will seek to identify and take advantage of opportunities to improve their processes, products and services.
Therefore, in order to remain competitive and relevant to the market, it is their obligation to learn how to promote continuous improvement.
Do you know what the continuous improvement cycle is?
You will find the answer to this question in the following guide, that also includes:
- What is the main objective of continuous improvement;
- Advantages of implementing continuous improvement in business administration;
- What are the main types of continuous improvement;
- What are the main tools for promoting continuous improvement;
- How to implement the continuous improvement cycle in your company;
- Continuous improvement: inspiring examples.
Concept: what is continuous improvement?
We can define the concept of continuous improvement –from an organizational point of view– as a set of actions that a company puts into practice with the purpose of continuously optimizing the improvement of processes, products and services.
This means that the company is constantly measuring and analyzing the way it performs its tasks; searching for failures, delays and bottlenecks that can be solved, thus leading to more efficiency and productivity.
It is not hard to understand what continuous improvement is if you see it as a constant search for opportunities of improvement. It is also a philosophy incorporated into the organizational culture of a company that seeks to improve its performance.
What is the principle of continuous improvement?
For Edward Deming, one of the pioneers and considered to be the great master of continuous improvement, its principle is to practice quality from the beginning of the manufacture of a product or delivery of a service, going through all of its stages.
As a consequence, theoretically, the need for a final inspection– which only detects failures after they have already occurred– would be eliminated. In addition, constant purposes must be established with focus on improvement; in order to make the organization competitive and active in business, in an economically sustainable way.
What is the main objective of continuous improvement?
Continuous improvement’s mission is to enable constant assessment of the quality of products and internal processes, in order to identify gridlocks, reduce waste and increase efficiency.
The main objective of continuous improvement is to allow the company to always perform its activities in the best possible way, generating greater value for the final consumer.
What are the main types of continuous improvement?
There are different types of continuous improvement that you can implement in your company. The main ones are:
- Continuous improvement for internal processes: focus on mapping the nuances of specific internal processes in order to correct failures and make changes capable of making them even more optimized;
- Continuous improvement for products: the goal is to constantly evaluate products and make iterations that make them more efficient.
- Continuous improvement for services: the intention is to improve the quality of services offered to customers.
Advantages of implementing continuous improvement in business administration
The benefits of implementing a cycle of continuous improvement to processes, products or services are countless. However, we highlight here some of the main reasons for adopting this culture within the daily management of your organization.
1. Greater incentive to work as a team
To promote continuous improvement, it is necessary that the employees know how to (and be willing to) work as a team.
Bringing together professionals with different skills and points of view will help to have more clarity of the problems faced and also find the most effective solutions.
2. Facilitate new employees onboarding
With the implementation of continuous improvement, it is possible to standardize processes. This favors the onboarding of new talents and who they will be able to perform their tasks according to previously defined quality standards and methodologies.
3. Increase in productivity
The continuous improvement cycle motivates teams to become more productive, doing more with less.
Your company’s productivity can be affected by several factors, here the eight biggest accomplices of unproductivity:
- Wanting to do a lot of things at the same time
- Don’t turn away from distractions
- Be a perfectionist
- Stay seated all day long
- Having trouble saying no
- Working beyond the limit instead of resting
- Constantly checking email messages
4. Cost reduction
Speaking of “doing more with less”, continuous improvement makes it possible to better identify gaps, which contributes to a significant reduction in operational costs.
5. Better risk management
Dedicating yourself to promoting processes’ continuous improvement, also ends up being a way of better managing risks, which allows the company to deal with them in a more calculated and prudent way.
What are the main tools for promoting continuous improvement?
There are several tools that you can use to promote the constant growth of your company’s processes, products and services. They favor innovation and the delivery of even more value to your customers.
You may already know or have heard about some of the continuous improvement tools which we are going to describe below. Continue reading and find out how they can help you implement continuous improvement.
1. Business Processes Management (BPM)
Business Processes Management is a tool that allows you to analyze the most relevant processes of a company and discover how to conduct them in more efficient and effective ways.
In order to do this, a mapping of these processes is carried out by using flowcharts that help to identify points that could be improved.
Afterwards, the flowcharts are redrawn, correcting the gaps found. Continuous monitoring of each process is done and, if necessary, they will be redesigned once more.
The BPM tool it’s also helpful to visualize tasks, those responsible for them and the inputs and outputs of each process more clearly.
2 – GUT Matrix
The GUT Matrix facilitates decision making, as it establishes the demands’ priorities. To do so, you need to evaluate three elements:
Gravity: How much can this specific task impact the others? If it has to be delayed, will it affect any other areas in the company? Rate the impact as follows:
- Not serious;
- Less serious;
- Serious;
- Very serious;
- Extremely serious.
Urgency: How long can this problem wait for a solution? Here you must define deadlines, as some issues might be very important yet not necessarily urgent. Ask yourself: does this issue need an immediate solution? Rate your tasks as follows:
- It can wait;
- Less urgent;
- Urgent;
- Very urgent;
- Demands an immediate solution.
Tendency: Make sure whether the task being evaluated tends to get worse. If so, does the worsening tend to become a big problem in a short period of time? Use a scale to rate as follows:
- No possibility of change;
- It will take a lot of time to get worse;
- It will get worse in a medium term;
- Short term to get worse;
- It can get suddenly worse.
As a complement to the GUT methodology, you can also use the “BASICO” approach.
- Benefits to the company;
- CoverAge;
- Employees Satisfaction;
- Investments needed;
- Customers;
- Operations.
Assign a score from 1 to 5 to each criteria and then define what should be prioritized to ensure continuous improvement.
3.Continuous improvement and Kaizen
Kaizen is one of the lean manufacturing tools,methodology developed in Japan in the early 1950s, as a way of trying to rebuild the country, which was devastated at the end of World War II.
Today, continuous improvement and Kaizen are practically synonymous, as there are explicit relations between the two methodologies. This happens since lean tools are used by different types of companies and processes.
Kaizen means “change for the better”. It serves to promote continuous improvement on personal, professional and business and follows the philosophy that tomorrow can always be better than today.
To apply Kaizen, you must:
- Focus on eliminating waste and creating value;
- Standardize processes;
- Count on a well-trained team;
- Eliminate waste and produce only what is needed;
- Optimize the use of equipment.
4 – Ishikawa diagram
The Ishikawa Diagram is a continuous improvement tool that aims to find the root cause of a problem. To do so, “6 Ms” are analyzed:
- Method
- Material
- Manpower
- Machinery
- Measurement
- Mother Nature
The idea is to understand how each of these six elements contribute to a specific problem. Maybe your business model does not include all the 6 Ms; if so, you can make the necessary adaptations.
5.PDCA Cycle
Another classic tool for promoting continuous improvement is the PDCA Cycle. It consists of 4 steps that must be carried out in a cyclical way so that a certain business process can be constantly enhanced.
The steps are as follows:
PLAN: to plan objectives and methodologies to face the problems.
DO: to put the plan into practice, implementing the solutions.
CHECK: to verify whether the results obtained with the implementation of improvements are in line with expectations.
ACT: to make the necessary adjustments based on what was observed during the “check”.
How to apply the cycle of continuous improvement in your company?
Now that you know the types of continuous improvement and the main tools that you can use to apply them, it’s time to check out some tips that will help you drive the implementation of continuous improvement in your company.
1. Map your current processes
Mapping is a practice that will allow you to identify problems and improvement opportunities in the analyzed processes.
For this, you must define the start of a process and also its end, in addition to all the intermediate activities, as well as the options available in the flow of activities that rely on the decision-making process.
That way, you can create a process flow diagram.
2. Find the root cause of the problems
To improve your processes, products or services, you need to tackle the root cause of the problems that are preventing good performance. It can be either through the Ishikawa Diagram or the 5 Whys methodology.
Don’t know how to find the root cause of your problems? Check out this video on YouTube:
3.Analyze performance indicators
KPIs are valuable metrics that will allow you to have a clearer and more objective view of the performance of the aspects you want to improve in your business.
To better understand how to use performance indicators, be sure to apply one of the performance indicator tools on the market. They will be fundamental to the entire improvement process within your organization.
4. Suggest solutions and plan how they will be implemented
After understanding the identified problems, suggest the most appropriate solutions for them and create an action plan for implementation.
5. Implement the changes
In the next step, put into practice what was defined in your action plan. You can implement the solutions on a smaller scale, as a beta test.
If the results seem positive when analyzing the indicators, you may want to expand the scope of the changes until you reach the desired point.
6. Evaluate the results
Evaluate the results after implementing the solutions. The objective is to check if everything is now as expected and if there is a need for adjustments.
7. Standardize the new changes
Create a standard that will guide employees on how things should be conducted from now on. That way, you’ll have a new baseline to resume the continuous improvement cycle.
Examples of continuous improvement for you to get inspired
Now you know what continuous improvement is and why it’s important to guarantee a good and competitive performance for the company.
To end this guide, find below 3 success cases of continuous improvement implementation that will inspire you.
Examples of continuous improvement
1. Toyota
2. Amazon
3. Disney
Did you understand the importance of continuously improving business processes? The examples above are quite enlightening, and will certainly guide you.
STRATWS One is a software specially developed for you to create, analyze and share your performance indicators, which is of great value for anyone who wants to improve their processes.
Here are other advantages of this tool, chosen by more than a thousand companies and used by more than 180 thousand employees:
- Integrate people, operation and strategy;
- Find opportunities for improvement;
- Manage meetings and project portfolio;
- Increase productivity;
- Share KPIs and information with celerity and transparency;
- Enhance corporate governance;
- Apply meritocracy and visual management concepts to motivate and manage teams;
- Employ the main strategic planning methodologies, such as BSC, OKR and SWOT;
- Manage risks and analyze scenarios;
- Facilitate the information flow and communication between departments.
Start STRATWs One, Siteware’s strategic management software free trial. Talk to us.