3 examples of manufacturing KPI’s: Start tracking them!
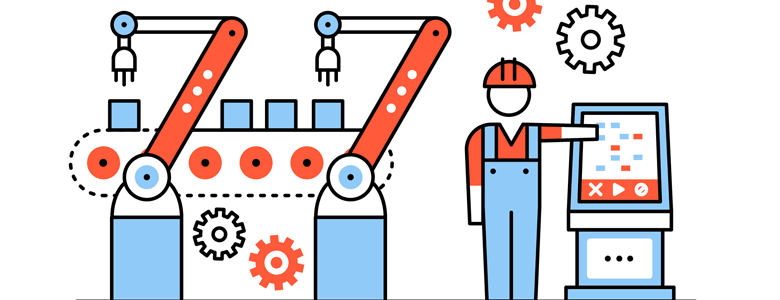
Conteúdo
The great icon of total quality and process improvement, W. Edwards Deming, “What cannot be measured, cannot be improved” is a truth that can never be overlooked by a good business manager.
Manufacturing KPI’s examples in industry are paramount in the measurement of product quality, process quality, inventory control, measuring manufacturing time, overall production, preparation time, customer and employee satisfaction, and much more.
The objective of Manufacturing KPI’s are to improve your company’s performance by helping you achieve the following benefits:
- Ensure an efficient strategy according to business goals;
- Ensure the quality of what is being delivered to the customer;
- Clearly define the cost-benefit ratio;
- Verify the performance capability of adopted resources.
In this post you will learn how to choose and also discover 3 Manufacturing KPI’s.
See also: What quality Manufacturing KPI’s examples should you use in your business?
How to choose Manufacturing KPI’s?
Each company has different processes and needs, as well as products and services.
However, most importantly the focus concentrates on industrial Manufacturing KPI’s examples that will measure the improvement of the customer experience towards your brand.
But how to access all this information?
At times like this it is best to use software to monitor these indicators in real time.
It will simplify understanding and evaluation of chosen indicators and help to capture, analyze and share them efficiently.
After all, information from simple spreadsheets does not give much confidence, when for example, making decisions and developing strategic planning.
For this, it is essential to rely on concrete, reliable, accurate and up-to-date information and data.
To put it all this into practice, you need to look for an established and experienced company.
Siteware has been developing the corporate performance management software that is now used by some of the largest companies in Brazil. Visit the company’s website to discover all the strategic management solutions.
3 important Manufacturing KPI’s
Measuring, analyzing and effectively improving activities through Manufacturing KPI’s is not as simple as it sounds.
While there are certain industrial productivity guides that work well for specific jobs, there are often several combinations of indicators needed to ensure that a business objective is achieved.
Industries are basically made up of two things: people and equipment. In that sense, the efficiency of equipment defines 50% of the operational success of an industry.
1- OEE (Global Equipment Efficiency)
The OEE (Overall Equipment Effectiveness) indicator measures the overall efficiency of equipment.
It is used to qualify and indicate how the manufacturing operation is performed and assists in improving the company’s maintenance and production processes.
Why overall efficiency?
Because it is based on the three key success factors of industry:
- Availability;
- Productivity;
- Quality.
There is no use for an industry to have equipment available if they are performing below expectations or producing too much, but without any quality.
The formula for calculating the OEE is quite simple:
OEE =% availability x% productivity x% quality
The first step is to calculate the percentage of availability.
The formulas for calculating each factor are:
- Availability = time produced / time available x 100
- Productivity = Actual Production / Theoretical Production x 100
- Quality = good parts / total parts produced x 100
And how do you know if the result is good or bad?
World Class OEE is greater than 85%. But that doesn’t mean that reaching that percentage means it’s ok.
There are some more detailed rules to follow:
- Availability must be greater than or equal to 90%
- Productivity must be greater than or equal to 95%
- Quality must be greater than or equal to 99.9%
- If you have reached 85% by following these rules, then you have achieved overall efficiency.
2- OLE (General Effectiveness of Labor)
Overall Labor Effectiveness (OLE) is an indicator that analyzes the cumulative effect that three factors of the workforce have on productivity (labor), thus enabling more accurate operational decisions and effective corrective action.
The three factors are:
- Availability: The percentage of time employees spend making an effective contribution;
- Performance: the amount of product delivered;
- Quality: The percentage of product produced fit for sale.
Through OLE it is possible to check aspects such as: reasons for machine inactivity, delays, absenteeism, etc.
Thereby, industry can assess the ability of employees performing their duties.
The calculation is:
- Availability = Operative Working Time / Planned Time
- Productivity = Effective Operator Output / Expected Output (or Work Pattern)
- Quality = Total salable parts / Total parts produced
OLE = Availability x Productivity x Quality
3- OTIF (On Time In Full)
This is an important guide for improving order and service delivery, through which strict compliance will ensure customer satisfaction.
OTIF supervision will highlight any shortcomings throughout its complete ordering process, from the creation of an order to supply.
With it you can assess if “Answered / Not Answered”.
On time means meeting the commitment you have made to your customer on any day and time, and In Full means nothing was missing from the delivery (no material, no parts). Plus the products were within the agreed specifications. Any alternative from this means you did not deliver “in full.”
The calculation is: OTIF =% on time x% in full = (result)
Achieving 100% OTIF means that all customer orders were met on time and of the right quantity / specification.
Does this make it clear how to calculate these industrial production indicators?
One way to keep all these numbers within your reach is to use a simple-to-operate intuitive software like STRATWs ONE, that integrates teams and people, bringing greater governance, productivity, and improved results.
Revolutionize your business management with STRATWs One