Quality tools: 7 most commonly used, benefits and how to apply them
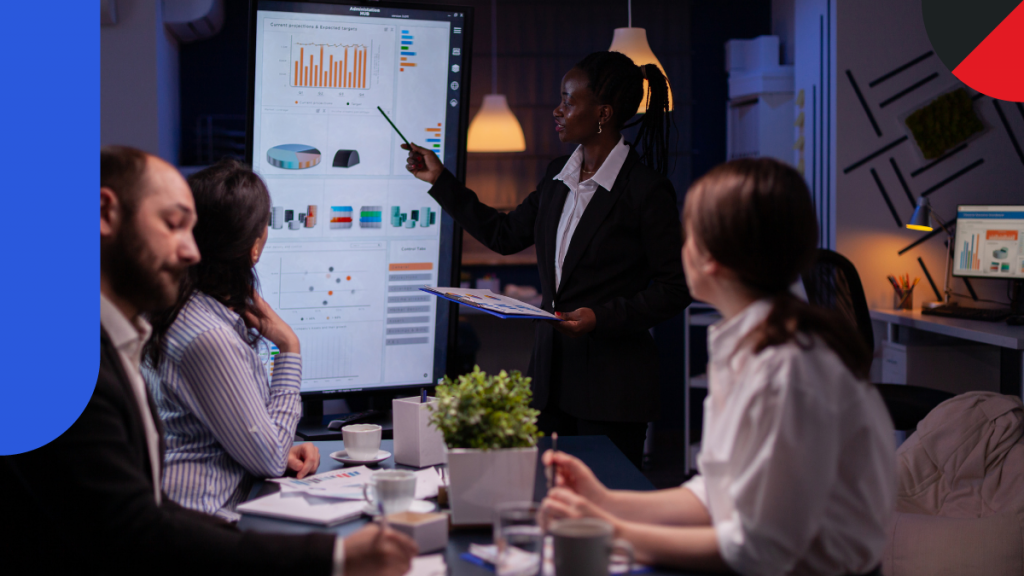
Conteúdo
The pursuit of quality to meet customer needs is no longer a competitive advantage but rather a necessity for brands to survive in an increasingly competitive market. In this article, we will delve into quality tools. Have you heard of them?
Improving the quality of a company’s solutions has a positive impact on all other processes, such as supply chain management, customer service, and, of course, strategic planning.
Discover the main essential tools for your company’s strategic planning!
It is crucial to understand which quality tools will bring about effective and noticeable improvements in your business procedures.
These tools are simple yet highly powerful, adaptable to any business setup. They are easy to use and streamline data collection, analysis, and visualization, making decision-making less complex than with other methodologies.
Keep reading and make the most of our insights!
What are the essential quality tools?
There are several quality tools at your disposal, but in this article, we will focus on 7 of them:
- Flowchart
- Ishikawa diagram
- Check sheet
- Histogram
- Pareto chart
- Scatter diagram
- Control chart
How to apply the quality tools?
Knowing these quality tools is crucial, but even more important is understanding how to apply them to your business. When used correctly, you can establish a culture of continuous improvement within your company, leading to constant enhancements in results.
Let’s take you step by step on how they work:
1. Flowchart
In a flowchart, we employ graphic symbols to depict the nature and flow of process steps.
These can range from simple, single-direction flows to complex processes that involve dual pathways.
Procedure:
- start with more general and less specific steps;
- observe the process and its functioning;
- analyze the sequence of phases and represent them in the flowchart.
Benefits:
- enhances understanding and simplification of processes;
- an extraordinary tool to support training and learning;
- identify problem areas and opportunities for improvement.
Read also: What is organizational decision making and 5 more tips on how to do it in practice
2. Ishikawa diagram
Also known as a cause-and-effect diagram or fishbone diagram, the Ishikawa diagram is one of the main quality tools. Its primary purpose is to identify, classify into useful categories, and display the possible causes of a problem or quality related aspect.
This visual tool aims to help teams pinpoint the root causes of the problems they face so they can be solved. The tool’s premise is that every problem has a specific cause.
Procedure:
- choose the problem to analyze and place it at the diagram’s vertex;
- divide its essence into categories;
- assign a branch from the main trunk emerging from the vertex where the problem is collected to each category;
- during brainstorming, divide each category into the simplest elements to resolve;
- use operational definitions;
- record positive sentences as goals and negative ones as problems.
Benefits:
- it is visual and uses a very simple format;
- facilitates problem resolution by breaking it into more manageable units;
- provides a very interesting overall perspective;
- helps in detecting root causes and possible reasons for variation;
- encourages participation;
- identifies areas where data collection is necessary;
- assists in quality management.
After completing the Ishikawa diagram, you can develop an action plan to resolve the identified problems.
Check out an example:
3. Check sheet
This quality tool simplifies process monitoring by providing valuable insights into common deviations and overall errors. Its main goal is to aid data collection, which is based on formulating questions such as where, what, who, and how.
Due to its user-friendliness, the check sheet is one of the most commonly used quality tools in large companies. It can be employed to identify defects in your product or service.
Procedure:
- collect data and provide historical records;
- record collected information individually;
- combine data to determine total and most frequent defect or error rates;
- record data collection methods used;
- create a check sheet template for each specific purpose.
Benefits:
- structured and easy to understand;
- well-suited for data collection and analysis;
- a versatile tool easily adaptable to various purposes.
4. Histogram
This chart is used to display frequency distributions or how often each different value appears in a data set. It is represented by a bar graph showing the data distribution, providing an instant visual of process data. It is one of the quality tools that aids real-time analysis.
Procedure:
- count the number of data points;
- summarize on a record sheet;
- calculate the data range;
- set the number of intervals based on Sturges’ rule;
- calculate the width of each interval;
- determine the starting points for the intervals;
- count the number of data points in each interval;
- apply the data to a control chart format;
- add a title and legend.
Benefits:
- allows for trend observation, facilitating anomaly detection;
- accurately represents variability and value dispersion;
- applicable to both continuous and discrete variables;
- especially useful for large samples;
- valuable as a communication tool;
- recommended as decision support.
5. Pareto chart
The Pareto chart is one of the most renowned quality tools worldwide. Also known as a Pareto diagram, it displays, in a bar chart, the most significant factors through root cause analysis.
Furthermore, it visualizes, in a bar graph, which factors are the most critical, following the 80/20 rule, which states that 80% of defects are concentrated in 20% of processes.
Procedure:
- record the data;
- classify the collected data;
- define the significance of the vertical and horizontal axes;
- provide a graphical format for the available information;
- perform the necessary calculations;
- add a cumulative line;
- include a title, legend, and date.
Benefits:
- helps focus on causes that will have a greater impact when resolved;
- provides a quick and straightforward overview of the relative importance of issues;
- prevents some causes from worsening while attempting to resolve others;
- its highly visible format serves as an incentive to pursue further improvements.
6. Scatter diagram
A scatter diagram is used to study and identify the potential relationship between changes observed in two different sets of variables.
This quality tool assists in determining the cause and effect relationship in terms of quality by examining the vertical and horizontal axes.
Procedure:
- collect data from two different groups and create a summary table;
- draw a chart and label the horizontal and vertical axes. It is common to assign causes to the X-axis and effects to the Y-axis;
- represent data pairs on the chart;
- interpret the scatter plot in terms of direction and strength.
Benefits:
- helps identify relationships between process transformations;
- facilitates the search for its causes;
- simplifies the establishment of action priorities.
7. Control chart
A control chart is a statistical quality tool that helps differentiate variations in processes caused by common factors from those originating in less standardized sources.
It enables the study of how a process changes over time.
Procedure:
- select the group size to be controlled;
- enter the data corresponding to the measured variables;
- identify any deviations. Measure again and reanalyze.
Benefits:
- helps verify the impact of each element of a system on the total;
- aids in process improvement;
- allows monitoring variations processes undergo over time;
- makes it possible to distinguish between variations caused by common factors and those due to more specific and less routine ones;
- facilitates evaluating the effectiveness of changes;
- is an appropriate tool for reporting process performance.
Next steps
Now that you are familiar with the quality tools, put them into action to achieve significant process improvements in your company.
If you want to closely monitor your business indicators, identify improvement opportunities, achieve the results your company wants, and utilize quality tools, consider our corporate performance management software, STRATWs One.
Revolutionize your company’s management with STRATWs One: